Pumping Mixer
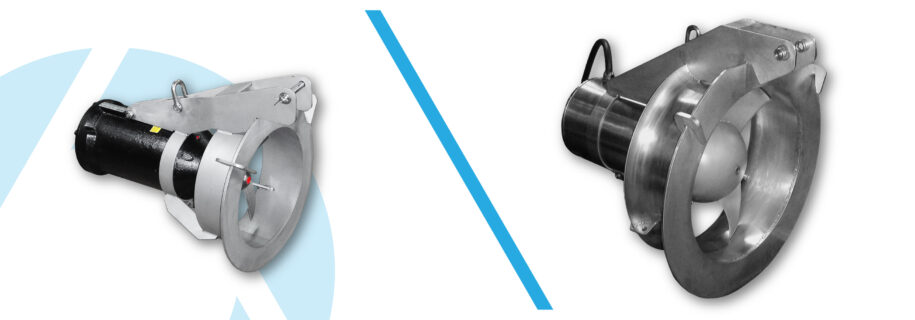
- pumping liquids between tanks with equal levels.
MZP mixer motor power: 0,37-2,2 kW
MKP mixer motor power: 1,5-5,5 kW
Pumping capacity: up to 80-810 m3/h
Flange size for MZP mixers: DN 150-300 mm
Flange size for MKP mixers: DN 350-600 mm
Max immersion depth: 10 m
Propeller mixers for operation in total immersion, equipped with coupling flanges that enable automatic attachment to the flanges of penetrations in tank walls. Standard MZ and MK submersible mixers, after minor modification, can operate as MZP and MKP pumping mixers cooperating with PMP guides equipped with flanges coupling with the pipeline flange or culvert through the tank wall. Pumping mixers are used to pump liquids between tanks with equal levels. The pumping capacity is proportional to the power of the mixers and can be additionally adjusted using an inverter.
The BIOX production offer includes two types of submersible pumping mixers differing in type and power range:
- MZP mixers (cast iron or stainless steel body),
- MKP mixers (stainless or acid-resistant).
Where increased corrosion resistance or greater device power is required, MK Turbo mixers are used. All external elements of these mixers are made of stainless steel, and a modern turbine propeller rotor ensures the highest pumping efficiency.
Control system – mixers can be equipped with a control cabinet, the basic variant of the cabinet includes protection against motor overload, phase loss, accidental change of phase sequence and the CR-3 signaling device. Of course, we can design and implement any control according to the customer’s guidelines; complex control systems are based on an inverter. The protection level of the cabinets – IP65 allows them to be used outdoors
Electric motor protection:
– temperature control sensor – thermistors, built into the stator windings of the mixer motor, react when the safe operating temperature is exceeded. This protects the engine from damage due to overheating.
Temperature sensors should be used in engines subject to overheating. This applies to engines operating in places with elevated ambient temperatures (>40°), engines exposed to overloads, engines exposed to frequent or heavy starts, and engines in which cooling is weaker than standard.
For most submersible mixer motors there is no particular need for built-in thermal protection, assuming that the standard motor protection, in particular overload protection, is working properly. During operation, the mixers are intensively cooled by the liquid flowing around them and usually operate at temperatures much lower than permissible.
– water presence sensor in the oil chamber – A sensor with a probe in the oil chamber signals the presence of water in an amount greater than the permissible amount and the need to immediately change the oil combined with assessing the condition of the seals based on the analysis of the drained oil.
In most cases, mechanical face seals used in submersible mixers ensure complete tightness. However, seal manufacturers reserve the possibility of minimal leaks occurring in certain circumstances. Small amounts of water dissolve in the oil or create an emulsion that further works perfectly with seals. Larger amounts of water, which the oil is no longer able to absorb, accumulate in the lower part of the chamber and also do not affect the operation of the seals. Water from seal leaks is removed during periodic oil changes.
– moisture sensor in the engine compartment – During the final assembly of the mixer, an insert is placed inside the engine to absorb moisture from the air trapped in the engine compartment. This avoids moisture and condensation inside the engine.
The moisture sensor signals the presence of moisture inside the engine compartment caused by a leak. The activation of this sensor is an indication that the mixer should be immediately inspected to determine the cause of the leak.
– integrated CR-3 signaling device – Probes and security sensors built into the mixer can be operated by the integrated CR-3 signaling device designed especially for submersible mixers of our production. If any of the protections are activated, the mixer operation is stopped and the appropriate diode on the CR-3 sensor lights up, indicating the reason for stopping the mixer.
The CR-3 indicator is necessary for the correct operation of the sensors when the mixer is equipped with all 3 sensors (engine temperature, presence of water in the oil chamber, engine humidity).
Pumping mixer guide
PMP pumping mixer guides are used for installation and subsequent operation of pumping mixers. The mixer is lowered to the working position using e.g. a crane.